What is GFRP Rebar?
Glass Fibre Reinforced Polymer
GFRP Rebar is a high-performance composite reinforcement material used as an alternative to traditional steel rebar in concrete construction.
It is manufactured using high-strength glass fibres embedded in a polymer resin matrix, offering exceptional durability, lightweight properties, and resistance to environmental challenges.
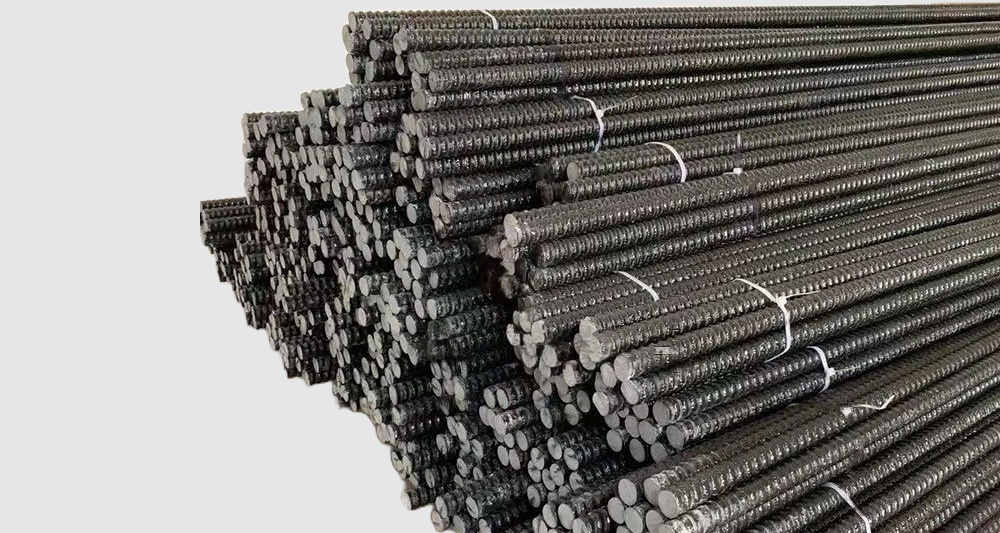
The composition of GFRP Rebar consist of two main elements:
Glass Fibres and Polymer Resin
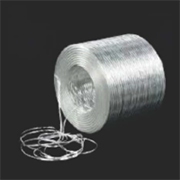
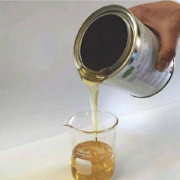
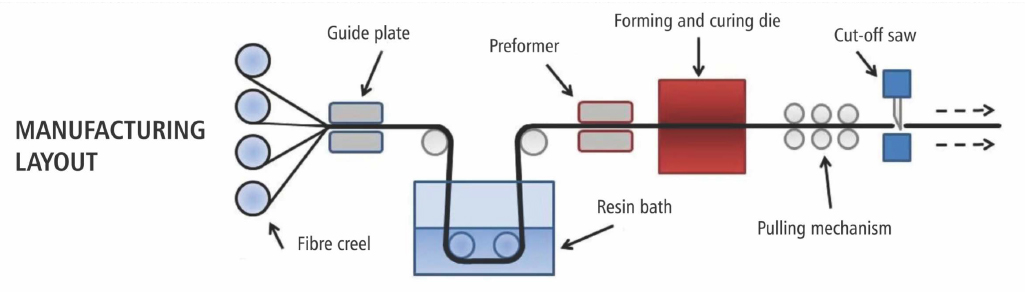
Types of GFRP Rebar -
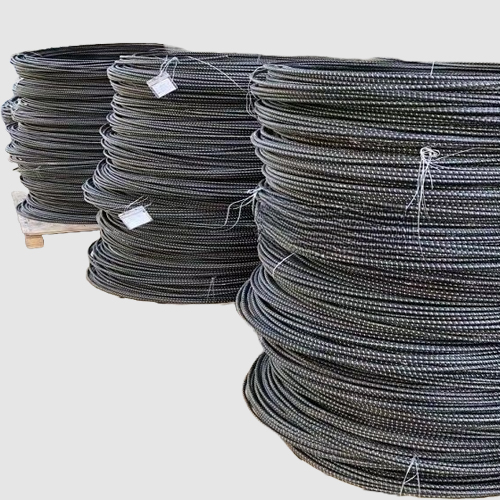
Coil Rebars
Length: Up to 50M / 100M
Diameter: 6 mm to 10 mm
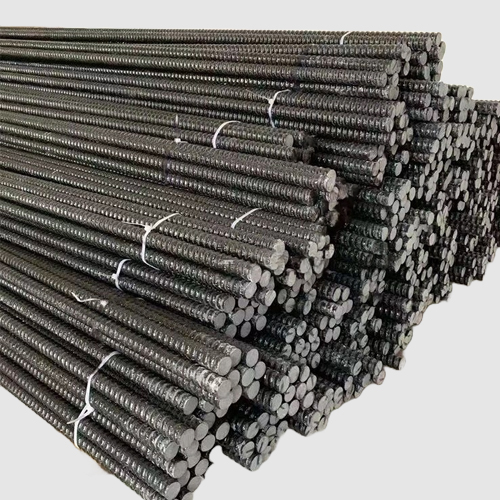
Straight Rebars
Length: Up to 12M
Diameter: 12 mm & above
Our Upcoming Products
Our upcoming GFRP Stirrup & Mesh products are engineered for superior strength, durability, and corrosion resistance. Designed for reinforcement applications in construction and infrastructure, these lightweight yet high-performance solutions offer enhanced flexibility and longevity compared to traditional materials. Stay tuned for innovative advancements in GFRP technology!
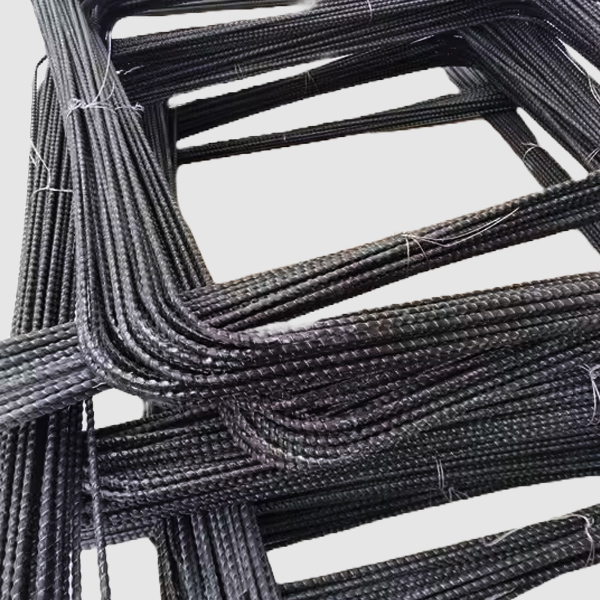
GFRP Stirrup Rebars
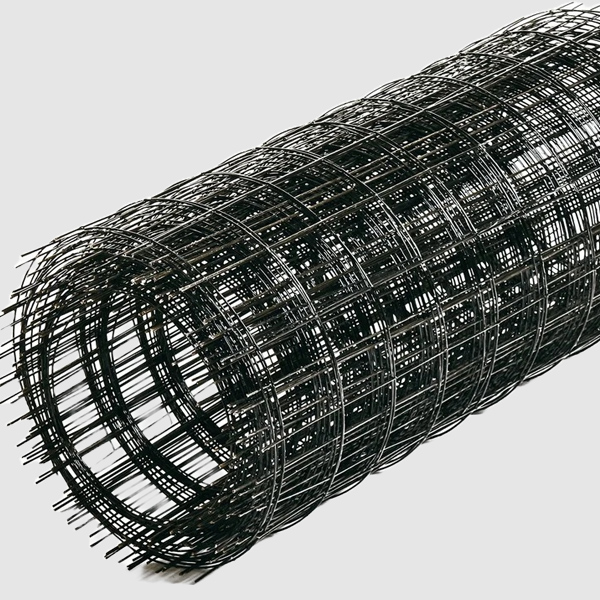